The right way to do it
by Alex Apostolov, Editor-in-Chief
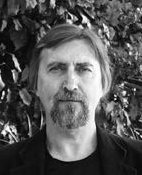
I have been at many different conferences around the world and have seen many presentations describing protection system maloperations and their terrible consequences. Watching the presentations in almost all the cases I thought that all of this could have been avoided if the protection devices or the complete protection system was properly tested.
The problem is that in many cases the testing process is not done the right way. This can be due to many different reasons such as following procedures developed sometime in the last century when the protection technology has been much different then what we have today, the lack of the right protection testing tools, loss of expertise and many others.
That is why we decided to dedicate this issue of the magazine to the testing of protection devices and systems.
When we talk about all of this many people are probably asking “So what is the right way to do it?” and as usual the answer starts with “It depends!”
To do it right we need to start by answering the following three questions in this specific order:
- What are we testing?
- Why are we testing?
- How are we testing?
The answer to the first question can be that we are testing a simple electromechanical relay, a multifunctional intelligent electronic device or a centralized protection and control system.
The answer to the second question can be that we are performing one of the following types of testing:
- Type testing
- Acceptance testing
- Interoperability testing
- Factory acceptance testing
- Commissioning testing
- Site acceptance testing
- Maintenance testing
- Others
Each one of these tests can be performed by different actors such as a manufacturer, certification body or the end user.
The answer to the third question depends on the answers to the first two questions, as well as some additional criteria such as:
- Regulatory requirements
- User requirements
- Established practice
- Available testing tools
- Recommendations from the manufacturer
One of the main issues that I have seen in many cases is that typically any of the tests performed for the testing types listed above falls within the category of positive tests.
These are also known as “test to pass” and involve testing a device or system under conditions where it is expected to operate correctly.
The goal is to confirm that the equipment functions as intended when used according to its specifications. Positive tests are designed to demonstrate that the system does what it is supposed to do. For example, testing a distance protection to ensure it operates correctly when tested under conditions corresponding to a fault within its specified zone of protection is a positive test.
However, this is not sufficient. It is also very important to include in the process negative testing, or as it is often referred to as “test to fail.”
This involves attempting to make the device under test to fail by pushing it beyond its normal operational parameters to ensure it can handle abnormal conditions or errors gracefully.
The purpose of negative testing is to identify how the equipment behaves under conditions of failure, such as handling invalid inputs or stressful environmental conditions. For instance, trying to make the protection operate when simulating a current transformer failure is a form of negative testing.
Another important issue is improving the efficiency of the testing which depends on the tools and methods being used.
For example, in some cases bottom-up or top-down approach should be used, as well as black box versus white box testing may be preferred. Standardized testing procedures and corresponding test plans can further help minimize the time and efforts, while at the same time improve the quality of the testing process.
“As ironic as it seems, the challenge of a tester is to test as little as possible.
Test less but test smarter.”
Federico Toledo