by Alexander Apostolov, USA
With the development of microprocessor technology, the protection and control systems became distributed, based on multifunctional IEDs.
We have gladly accepted this elevated level of functional integration without worrying much that we are putting all our eggs in one basket. And it is because the individual functions are not isolated but integrated in a sophisticated system that can survive the challenges of its environment.
Accepting the high levels of functional integration in our everyday lives now is transitioning into our professional lives as protection, automation and control specialists. We are already using for a couple of decades multifunctional intelligent electronic devices. This experience will make it easier to get to the next level – Centralized Substation, Protection, Automation and Control Systems (CSPACS).
What are we doing?
IEC 61850 is the standard that we can consider as the glue that allows us to combine the advanced computer and communication technologies into sophisticated protection, automation and control systems. Digital substations are becoming a reality in many countries around the world and are accepted as the standard for future substations for many major utilities.
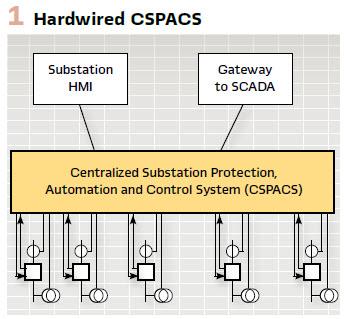
The availability of powerful industrial computers and real time operating systems are creating an environment supporting the next step in the evolution of digital substations – Centralized Substation, Protection, Automation and Control Systems (CSPACS).
This idea is definitely not new – it was first introduced half a century ago by George Rockefeller in his paper “Fault Protection with a Digital Computer” published in 1969 in the IEEE Transactions on Power Apparatus and Systems. The concept was implemented by Westinghouse which developed the first digital relay with the Prodar 70 between 1969 and 1971. It was commissioned in service on a 230 kV transmission line at Pacific Gas & Electric’s Tesla substation in February 1971 and was in service for six years. With the development of microprocessor technology, the protection and control systems became distributed, based on multi-functional Intelligent Electronic Devices (IED)s. However, at the same time Ontario Hydro in Canada developed an Integrated Protection and Control System (IPACS). Their analysis convinced them that when each device independently acquires and processes the power system signals from current and voltage instrument transformers, circuit breakers and disconnectors, tap changers, etc. in order to perform its assigned function it limits the efficiency of the system.
The first disadvantage is the cost associated with purchasing and installing each device acquiring power system signals independently. Wiring the same current, voltage and binary signals to multiple IEDs is costly and time consuming, something that was not acceptable to them. On top of that was the need for exchange of signals between the individual devices for the implementation of different protection schemes – something else that was typically done using hardwiring. That is why they decided to take advantage of modern microcomputers, digital signal processors, analog-to-digital converters, optical sensors and fiber optic communication technologies to acquire and process electrical power system signals in a new and more efficient way – in a centralized protection and control system.
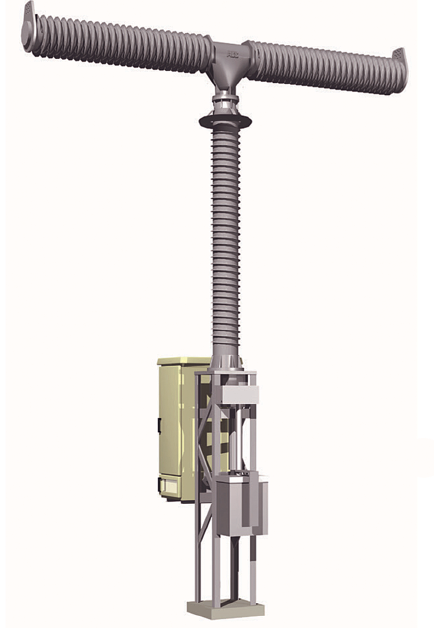
The concept was proven when the first integrated protection and control system was placed in service in July of 1994. All the system functions were enabled, but the protection functions were operating in a monitoring mode for a six-month period to verify that the system would not initiate incorrect trip signals. After the six-month monitoring period the different protection functions were gradually armed, thus proving that fully integrated substation protection, control, monitoring and recording is technically feasible and practical, providing a more efficient and flexible solution.
The IPACS can be considered as a pure centralized protection and control system, because it has direct hardwired – copper or fiber – interfaces to the substation equipment and conventional instrument transformers or optical sensors, while all the analog to digital conversion and digital signal processing is performed by the IPACS. Also, all the protection, control, monitoring and recoding functions are implemented in the central unit. (Figure 1).
About the same time a centralized integrated protection and control system for a small distribution substation was implemented by me in a universal, user programmable protection IED and presented at the Georgia Tech Protective Relay conference in 1995.
The higher level of functional integration achieved by such centralized systems definitely improves the efficiency of the protection and control system but does not eliminate all the problems that we experience in traditional hard-wired systems. Even that we save a lot by eliminating the hardwiring between all the different measuring, protection and control devices by integrating them in a centralized system, we still have the extensive hardwiring between the control house and the substation equipment, as well as issues such as current transformers saturation and open CT circuits.
With the development of IEC 61850, resulting in communications-based analog interfaces using streaming sampled values, as well as GOOSE based switchgear monitoring and control interfaces, it is clear that we are shifting towards a new generation of centralized systems that bring together the best of both worlds – the benefits of the digital substation and the efficiency of the centralized system.
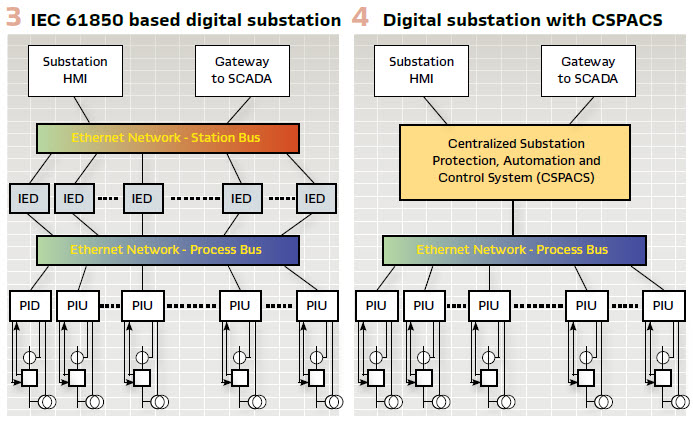
However, from a pure definition point of view the IEC 61850 based CSPACS is what we will call a hybrid system, because at least the digitalization of the analog and binary signals from the substation equipment is performed by the different process interface devices, while protection, automation, control and many other functions are running on the central substation computer.
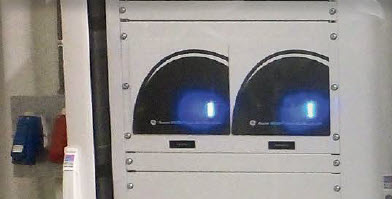
Why are we doing it?
The answer to this question is fairly simple – because our goal is to improve the reliability, security and efficiency of the electric power grid of the 21st century. Many utilities around the world are facing a wide range of challenges, such as:
- Environmental challenges and high costs of building new substations, especially the land and control house
- Significant expenses for purchasing equipment, its transportation, construction and installation
- Labor intensive process of connecting primary substation equipment and multi-functional IEDs
- Increased installation and commissioning costs
- Labor intensive mapping of data from multi-functional IEDs to substation HMI which increases engineering costs and is prone to human errors
- Limitations with the number of inputs and outputs of multi-functional IEDs which may require the use of additional auxiliary equipment, resulting in increased costs, reduced reliability and degraded protection scheme performance
- Proprietary communications interfaces between IEDs from different manufacturers do not support interoperability
- Unsupervised hard-wired interfaces between relays do not provide indication about the failure of an interface which may lead to a failure to operate when necessary and require maintenance testing
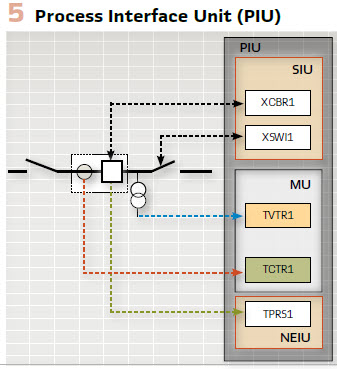
- Safety concerns related to possibility for open CT circuits causing high voltages that can hurt or even kill employees
- Labor intensive maintenance testing requiring traveling to substation locations
- Outages for testing of protection IEDs or schemes which reduce electric power system reliability
- CT saturation and CCVT transients may result in incorrect operation of protection functions
- High penetration of different types of Distributed Energy Resources (Figure 3).
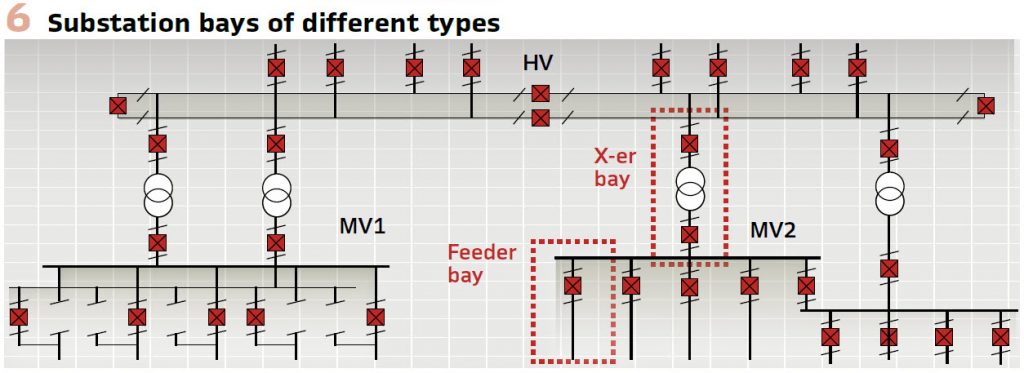
The development of IEC 61850 Edition 2 and the Smart Grid related extensions, combined with integrated switchgear, such as disconnecting circuit breakers (DCB) with integrated optical sensors (Figure 2) provide us with tools that can help us solve many of the above listed issues. Transitioning from the traditionally distributed digital substations towards centralized hybrid substation protection, automation and control systems will further improve the reliability, security and efficiency of the system.
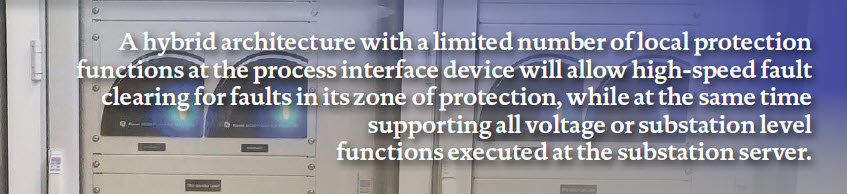
How are we doing it?
Considering the definition of pure centralized protection and control system introduced earlier in the article it is clear that in the case of IEC 61850 based systems we will always talk about hybrid systems. This is because the processing of the analog and binary signals from the substation equipment in the yard is performed by different devices that are connected to the central unit using fiber optic cables. These devices we can call process interface devices (PID).
The process interface devices can be with different levels of complexity depending on which process interface functions they are implementing.
In this article we use the following naming conventions:
- Merging Unit (MU) converts analog signals (currents and voltages) into time-synchronized streams of sampled values according to IEC 61850-9-2 of IEC 61869
- Switchgear Interface Unit (SIU) provides a binary status and control interface for circuit breakers and switches
- Non-Electric Interface Unit (NEIU) converts analog signals from non-electric sensors into time-synchronized streams of sampled values according to IEC 61850 9-2 or GOOSE messages according to IEC 61850-8-1
- Process Interface Unit combines two or more of the functions listed above (Figure 5)
- Process Interface IED (PIIED) combines the functionality of a PIU with local protection, control and/or other non-interface functions
The different process interface devices communicate with the central substation device using the required IEC 61850 services. The communications architecture depends on the specifics of the substation and the requirements for performance, reliability and security. Redundancy protocols such as PRP are used to improve the reliability of the system.
All components of the CSPACS are time-synchronized based on IEC 61850-9-3 (a PTP profile)
Engineering of CSPACS
The engineering of any IEC 61850 based digital substation is based on the System Configuration Language (SCL) defined in IEC 61850-6. The introduction of the IED Specification Description (ISD) file and the development of the virtual IED (vIED) concept allows the engineering of a digital substation independent of the actual implementation.

The engineering process should be based on an object-oriented design approach according to the standardized protection, automation and control schemes for the different types of bays in a high voltage substation. Figure 6 shows a simplified one-line diagram of a substation and several types of bays, such as a transformer bay or a distribution feeder bay.
Each of the standard bays should be associated with a virtual IED containing logical devices representing the implemented functions.
Figure 7 shows an example of a virtual IED for a distribution feeder. It contains four logical devices representing the main function groups:
- LD PROT – this is the distribution feeder protection function
- LD CTRL – this is the distribution feeder control function
- LD MEAS – this is the distribution feeder measurements function
- LD RCRD – this is the distribution feeder recording function
Each of these logical devices may have a single layer or nested hierarchy depending on the complexity of the implemented functionality. In the example the LD PROT contains an overcurrent protection sub-function LD ocp, which then contains a ground and phase overcurrent sub-functions (LD gnd and LD phs). The overcurrent protection function elements (PIOC and PTOC) are contained in these logical devices.
The LD PROT also contains the trip conditioning (PTRC), breaker failure (RBRF) and auto-reclosing (RREC) logical nodes. Each virtual IED is instantiated within the project as many times as is the number of bays of a specific type within the substation.
The next step in the engineering process is the definition of the signal flow based on the external reference in SCL which is represented by InRef and BlkRef in the logical nodes data models.
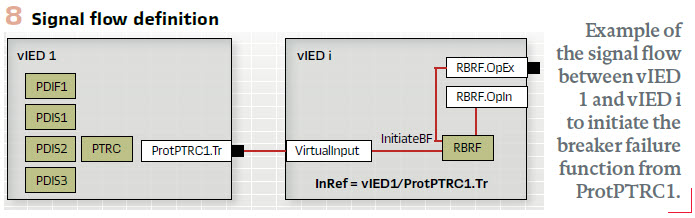
Figure 8 shows and example of the signal flow between vIED 1 and vIED i to initiate the breaker failure function from ProtPTRC1.Tr into the virtual input InRef of RBRF of vIED i. This signal flow in this case will be executed over the digital data bus of the substation server, but it also needs to be included in the GOOSE message published over the substation LAN to be visible by the process interface devices and the test system. The engineering of the system should also include the engineering of the test system.
An important part of the design of a centralized digital substation is to ensure its reliability considering the concentration of all protection, control, measurements, monitoring, recording functions in a single substation level server. That is why it will be necessary to install redundant servers operating in parallel.
In critical substations it may be necessary to install a third server operating in a standby mode which my be enabled in case of failure or upgrade of one of the two main servers
Testing of CSPACS
The testing of CSPACS depends on the purpose of the test. It has many similarities, but also some differences in comparison with distributed digital substations.
While the testing of the different functions of CSPACS during the design and acceptance testing is not very different from the functional testing of multifunctional IEDs with high-levels of integration in digital substations, the more challenging testing is for commissioning and maintenance.
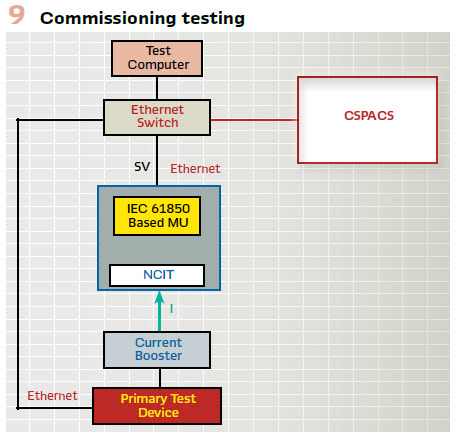
During commissioning one of the most important goals is to ensure that the interfaces to the process are properly connected. This requires primary injection as shown in Figure 9. The test system then compares the reported by the measuring function elements MMXU magnitudes and angles of the injected currents and voltages to ensure that all connections are correct.
The functional testing of the different protection functions of the CSPACS should be based on the “White box testing” method which is not only concerned with the operation of the test object under the test conditions, but also views its internal behavior and structure. In the case of protection system, it means that it will not only monitor the operation of the system at its function boundary, but also monitor the exchange of signals between different components of the system visible as data objects or attributes published by the different logical devices of the CSPACS.
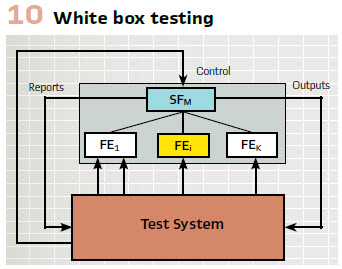
The testing strategy allows us to examine the internal structure of the test object and is useful in the case of analysis of its behavior, especially when the test failed.
Considering that according to the current definitions of IEC 61850 the control of the subscription to simulated values by the test system in the substation, it may be challenging to isolate individual function elements for testing in a live substation. In this case the TstRef (Figure 11) allows us to directly point to data coming from test equipment that is simulating a specific system condition, without pretending that it is a process interface device or other equipment in the substation.
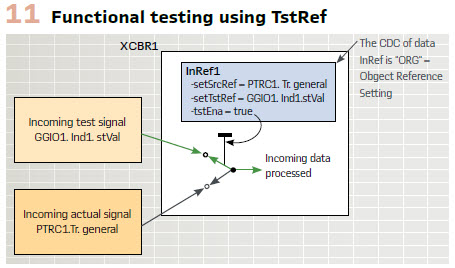
With CSPACS it is possible in some cases to avoid the need for connecting test equipment to the substation local area network when the testing involves only protection function elements implemented in a virtual IED. This will require an integrated virtual test set with current, voltage and other signal simulators represented by the corresponding logical nodes and used in the TstRef.
The availability of such testing tools will also allow remote testing by qualified specialists based on Role Based Access Control (RBAC).
The benefits of CSPACS
The business case for switching from distributed to centralized digital CSPACS is based on the additional benefits such a system brings on top of the established benefits of a digital substation:
- Improved reliability because of the reduced number of system components
- Improved cyber security because of the reduced number of targets to attack
- Reduced size of the control house
- Simplified communications architecture
A hybrid architecture with a limited number of local protection functions at the process interface device will allow high-speed fault clearing for faults in its zone of protection, while at the same time supporting all voltage or substation level functions executed at the substation server.
Biography
Dr. Alexander Apostolov received his MS degree in Electrical Engineering, MS in Applied Mathematics and Ph.D. from the Technical University in Sofia, Bulgaria. He is Principal Engineer for OMICRON electronics in Los Angeles, CA. He is an IEEE Fellow and Member of the PSRC and Substations C0 Subcommittee. He is past Chairman of the Relay Communications Subcommittee, serves on many IEEE PES WGs. He is a member of IEC TC57 WGs 10, 17, 18, 19, Convenor of CIGRE WG B5.53 and member of several other CIGRE B5 WGs. He is a Distinguished Member of CIGRE. He holds 4 patents and has authored and presented more than 500 technical papers. He is an IEEE Distinguished Lecturer and Adjunct Professor at the Department of Electrical Engineering, Cape Peninsula University of Technology, Cape Town, S. Africa. He is Editor-in-Chief of PAC World Magazine.