Mital Kanabar, Canada, David MacDonald, Spain, and Sean Norris, UK, all from Grid Solutions
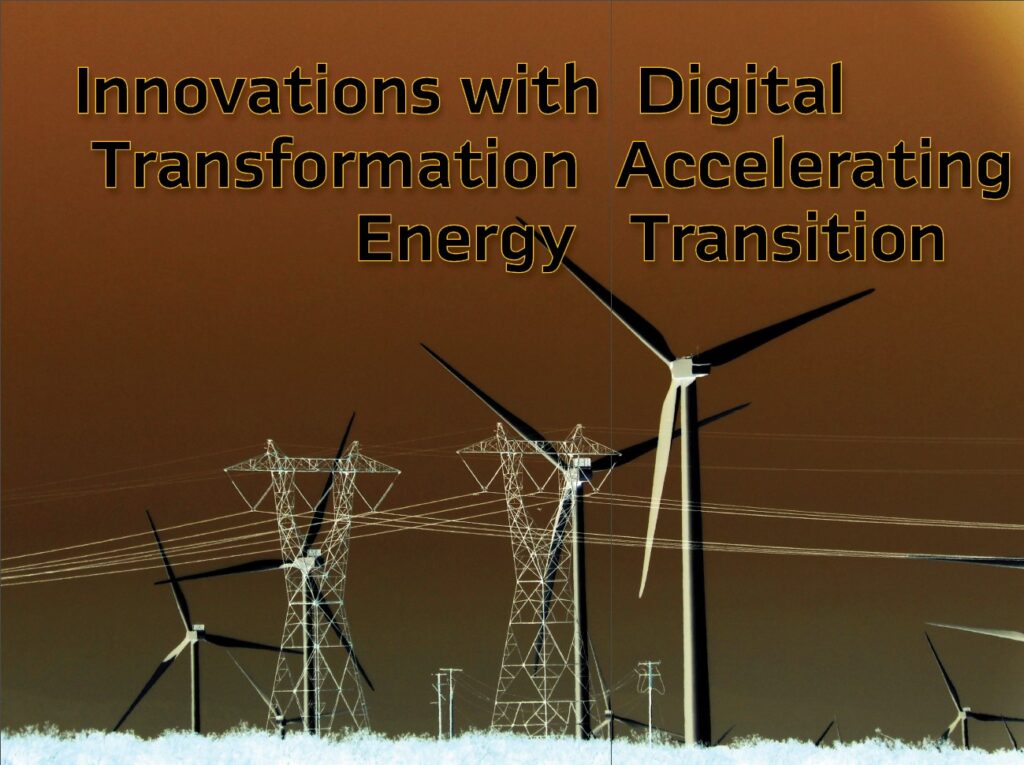
Grid Transformational Drivers of the Energy Transition:
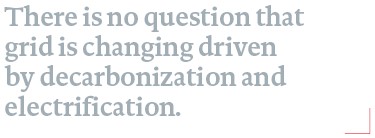
Decarbonization and Electrifications are the key drivers accelerating the energy transition in the industry, along with grid modernization of the aging infrastructure as well as external factors, such as, external weather, cyber risk and changes in policies & regulations, as illustrated in Figure 1. Energy industry is undergoing significant transition from fossil fuel to sustainable energy sources driven by decarbonization, also driven by UN’s Sustainable Development Goals (SDG) such as, climate action, affordable and clean energy initiatives. This transition needs to balance energy trilemma problem among energy security (incl. reliability and resilience), affordability or equity, and environmental sustainability.
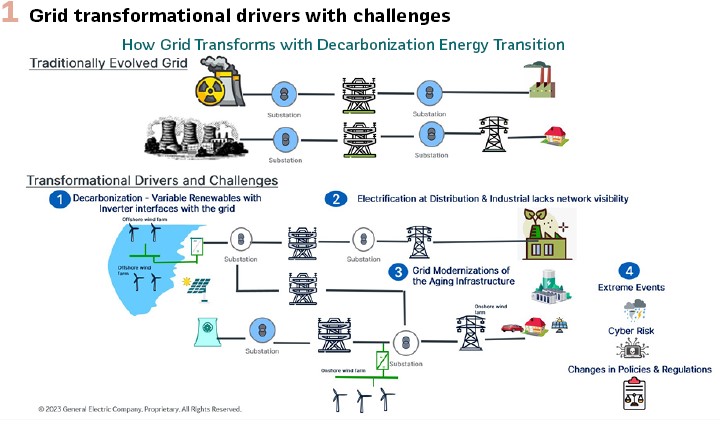
The energy transition is at hand, but its success relies on our ability to adapt our aging power grid infrastructure to support the entire ecosystem around it. Therefore, Protection Automation and Control (PAC) innovations with the digital transformation of the grid substation are crucial to evolving our technology rapidly enough to meet the world’s rising demands of green energy.
Electrical Energy Delivery Ecosystem Transformation
The electrical energy delivery has been largely evolving for over 100+ years. So, why now? In speaking with many global utilities and heavy power users, three clear factors have emerged as being driving forces: the need and push for decarbonization, the decentralization caused by the growth of renewables and DERs, and digitization–our ability to connect more assets and visualize more data than ever before. Digital transformation enabled by grid modernization technology in the transmission and distribution system will play a central role in the energy transition. The end-to-end electrical grid ecosystem transformation is illustrated in the Figure 2.
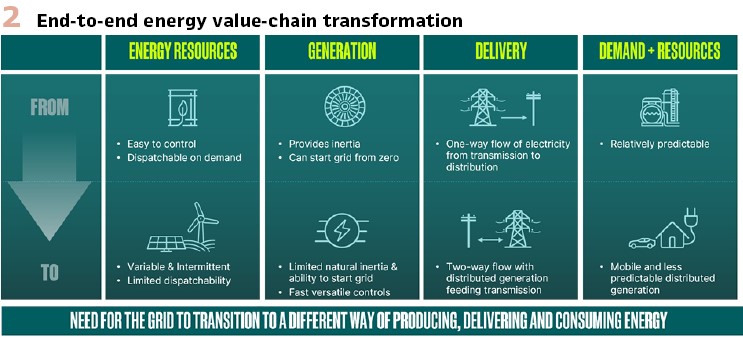
The electric power grid being part of the global energy networks plays a critical role either to enable or bottle-neck the energy transition. To address the speed and magnitude of the change driven by energy transition would require electric power grid to prioritize solutions for:
1) Improving grid performance and utilization with digital transformational solutions, incl. standardized digital substations across T&D; 2) Enhancing grid resilience and security during extreme weather or cyber events
3) Maintaining grid reliability and stability while allowing higher penetration of variable renewable energy resources, esp. at transmission network; 4) Build grid visibility and flexibility through distributed controls mainly at distribution level.
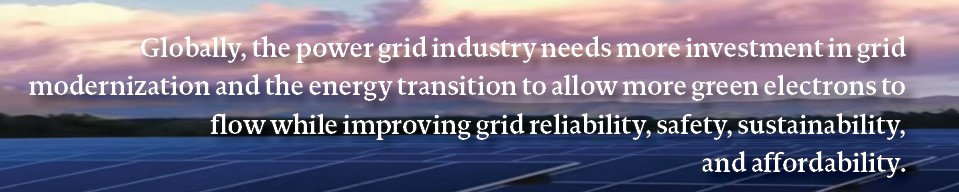
Distributed/Zonal Intelligence for the Changing Grid
This section presents a paradigm shift of moving centralized controls to more distributed intelligence controls as illustrated in Figure 3. Grid reliability and resilience are not only important from regulations perspective, but also supports with one the key aspects of Energy Trilemma, i.e., Energy security. With integration of more renewable energy resources are lower inertia distributed across wider regions across the grid. Overall system inertia is decreasing, which will reduce the system control reaction time. There will be need for a middle layer Automation & control between centralized control center layer and substation protection layer to take control across the regional level.
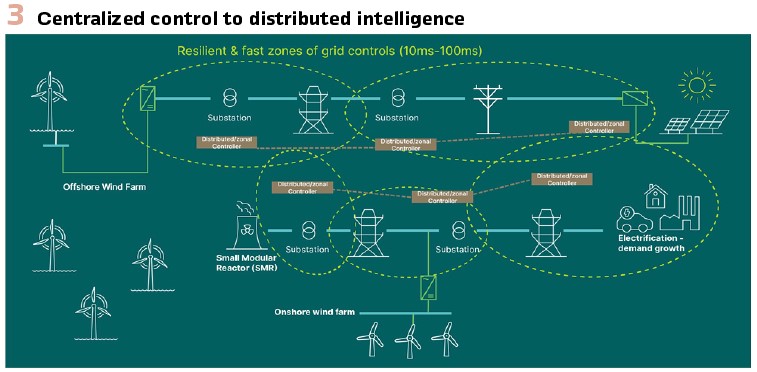
This middle layer can be achieved using Zonal control system which may use peer-to-peer R-GOOSE or client/server PMU/PDC architectures. Zonal control delivering grid reliability and resilience may require performing system studies to identify the performance requirements & local regulations.
With increased challenges and complexity of the grid of the future with many more available controls knobs (IBRs and flexible loads), a distributed control architecture shown on the right is needed, wherein, there are local zones (e.g., substations or large feeders) with more autonomous monitoring and control within the zone, and cooperative coordination across multiple such zones and the central grid orchestration in the Utility control room. New Distributed Energy Resources (DERs) and flexible loads provide new means to monitor and control the grid by coordinating their operation, i.e., provide new control knobs at the nodes with much faster and capable control authority with fast-acting Inverter-Based Resources (IBRs). This motivates a hierarchical approach with more distributed control architectures like Zonal control at the major regional substations. Temporal view of the same challenge and opportunity for zonal control is in the Figure 4. This is adequate and works well with a unified approach in today’s grid.
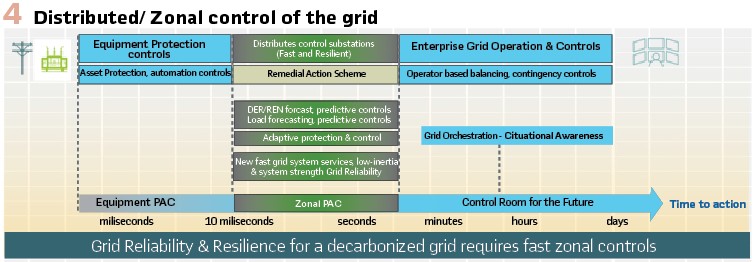
As shown in temporal view of the grid control, one end of the time-scale spectrum, there are the fast (milliseconds) local grid following (GFL) or grid forming (GFM) controls for the individual IBRs. At the other end of the spectrum is the conventional EMS, DERMS and ADMS using quasi-steady-state models and analysis/tools for day-ahead and intra-day planning, monitoring, and controls with conventional control knobs (e.g., tap changers, voltage regulators, capacitor banks), which are few and at critical locations, and controlled at relatively slow timescales (several minutes). With the growth of fast-acting (and variable due to weather fluctuations, e.g., solar PV) IBRs, there is a need for intermediate-time-scale dynamic coordination. Zonal control can address this critical and emerging gap for intermediate-time-scale supervisory control for coordination of controllable DERs and loads, as well as optimized coordination with the capabilities of ADMS and DERMS.
Digital Transformation of the Grid Substations
This section presents the digital transformation applied within the substation as well as outside the fence of transmission and distribution networks.
Software-defined Digital Substations: More and more utilities started investing into digital substation protection, automation, control (PAC) systems with grid modernization, new technology adoption with AI analytics. Digitalization allows data to be available for utilities to add significant value and optimize their asset management. Figure 5 shows the hierarchical architecture of a digital substation PAC system divided into three existing levels: process, bay, and station. Considering the technology cycles discussed earlier, the process level needs to “simplify” through digitization using open standard data sharing communication interfaces (i.e., IEC 61850-9-2LE and/or IEC61869-9/13). The bay level should be able to “converge” PAC applications with centralized substation protection systems.
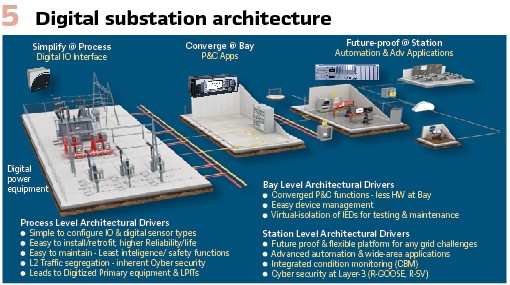
The station bus can be designed as “future-proof” with software-defined applications for the grid of the future. As the grid/substation evolves (such as through renewables penetration), the scalable substation control/automation application platform can allow future applications and solutions without replacing the hardware or platform software.
Multi-speed of Technologies for a Substation
The historical evolution of protective relaying technology has been significantly influenced by electronics and communication developments. The next generation of digital protective relaying is also receiving direction from evolving technology trends of the industrial internet of things (IIoT), virtualization, digital interfaces of combined optical CT/VT and circuit breakers, as well as digitized primary equipment. Figure 6 illustrates the differences in various technology evolution cycles related to the substation protection, automation and control system.
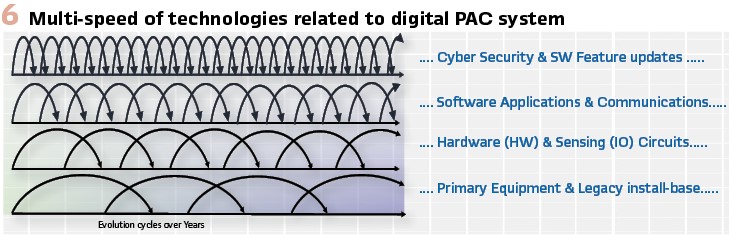
The technologies of primary equipment and legacy system install base cycles around several decades before they are migrated to next generation technology. The lifespan of ruggedized and digitized remote input/output hardware electronics including sensor circuits can be simplified and stretched to 1-2 decades. On the other hand, the cycles of software applications and communications technologies are typically evolving at a higher rate (several years); whereas cyber security applications and specific software/firmware may need updates annually or even on demand based on specific requests.
Software-Defined for the Changing Grid
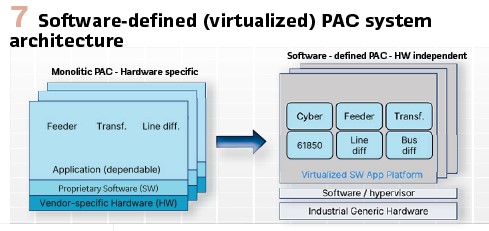
Figure 7 presents innovation driving software-defined or also known as, Virtualized, substation PAC platforms. The virtualized technology architecture has the potential to migrate mission-critical substation automation from native specific hardware platforms to virtual machines or containerized applications in an industrial generic hardware (which is substation certified).
Figure 8 provides the architecture of an advanced automation application system that allows a real-time operating system with a non-real-time Internet of Things operating system using virtual machine architecture. The hypervisor allows scalable multi-core CPU cores and execution of real-time grid logic along with a non-time-critical human-machine interface type of application.
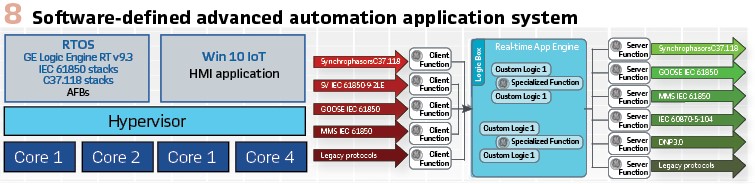
The advanced software-defined substation automation system will be using container-based architecture and a secure edge operating system lighter than typical virtual machines in terms of footprint and memory usage. They boot faster and use fewer resources than virtual machines. They can be deployed seamlessly across development, validation, and production and are easily portable across different computing environments. This system allows enhancement of grid reliability and flexibility to adapt to the changes that come with the integration of more renewable energy resources.
It is not so easy to add completely new functionalities during the lifecycle of an existing Substation Automation System. It requires visiting the substation and therefore incurs a significant time cost. Upgrading firmware remotely means incurring some duration of protection unavailability and some level of risk that the firmware update could fail without rollback to the previous image. Replacement hardware is required for a large variety of devices. This leads to centralized repositories of spares and therefore usually obliges the centralized specialist Protection and Control staff to attend to the low added value work of corrective maintenance.
Given that there are separate IEDs in each bay and in Transmission levels these can be four devices per bay, the sheer number of devices to be managed is challenging and requires some level of corrective maintenance. Protection and Control Replacement projects are necessary because of reaching the end of the hardware lifecycle but require complete reengineering and testing of the whole Protection and Control System.
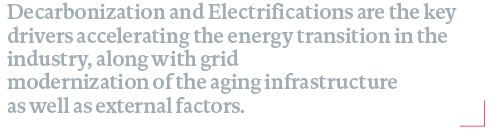
A Virtualized Protection and Control System is one in which the software is not fixed to the hardware but rather agnostic to the hardware. A middleware layer, consisting of a hypervisor, assigns those hardware resources such as RAM, Disk Space or CPU Cores to the Software Applications. In comparison to the devices whose functionality is fixed to hardware, Virtualized Protection Automation and Control (VPAC) Systems offer not just a compelling business case to interested utilities and industry actors but also a whole host of benefits:
- The Flexibility to add new functionality to the Substation Automation System without having to add new hardware
- The ability to upgrade or change not just the protection or control firmware but actually the complete application during the lifecycle of the hardware
- VPAC systems could become springboards of innovation because it would be so easy to remotely install and place new applications in test mode
- The convergence of hardware and the agnosticism that VPAC systems have towards the same, combine to greatly reduce the number of devices that would be required for Spare Parts. This means spare servers’ storage could be distributed geographically throughout the Utilities network and thus managed by localized Substation Staff rather than by specialist Protection and Control staff from a centralized location (who can dedicate their time to the high added value work of commissioning)
- Replacement projects, where the protection and control software can remain the same, become very straightforward in terms of engineering and testing. No change is required to the configuration whilst the only testing that should be carried out is that which pertains to the hardware itself such as the PTP or PRP interfaces and Hardware qualification
- Remote testing. The combination of the Process Bus, the IEC 61850 test mode concept together with the complete redundancy offered in VPAC systems makes remote and automated testing very practical
- Flexibility in VPAC systems means that utilities can license for the required PAC functions which they require and receive the same rather than many applications which would rarely be used
Nonetheless, VPAC systems represent a very significant paradigm shift from the status quo, of the same order of magnitude as the migration from electromechanical relays to modern microprocessor based digital relays whose functionality was also fixed to hardware.
In both cases there is a consolidation of devices, new failure modes, different maintenance practices and lifecycle management. Therefore, it is recommended to procure the entire VPAC system, including, generic hardware with vendor-provided software platform (including, hypervisor if needed), as well as integration of several PAC applications. For any change in the substation will mostly be software-change than the hardware, which can be used from vendor’s software service contract.
Adaptive Grid AI-enabled Analytics
Power grid networks and equipment infrastructure are monitored and controlled by edge devices with sensors and actuators with some level of intelligent analytics. As illustrated in Figure 9, the evolution of grid edge analytics innovations progresses from a reactive management strategy that responds to failures after they occur to a more autonomous future state with self-healing capabilities.
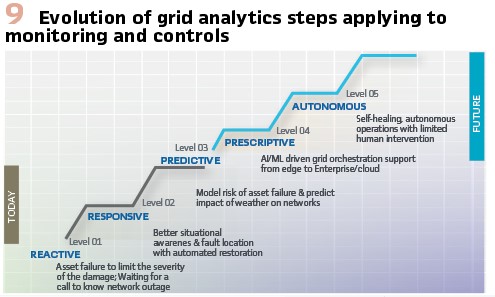
Most existing grid edge analytics are reactive to failures to limit damage, with limited responsiveness to restore automatically. The predictive stage may utilize system or asset models with a combination of physics and machine learning methods, including anomaly detection, classifications, and/or learned patterns.
Further grid innovations can be applied to suggest potential implications and recommended actions. Finally, the autonomous grid with self-healing capabilities would use edge-to-edge communications with very limited or no human intervention.
Physics-informed AI for the Digital Twin of the Digital Substation
One element of AI enabled Digital Twin technology, primarily used within the power industry for detection purposes related to cybersecurity and troubleshooting of the grid, as illustrated in Figure 10.
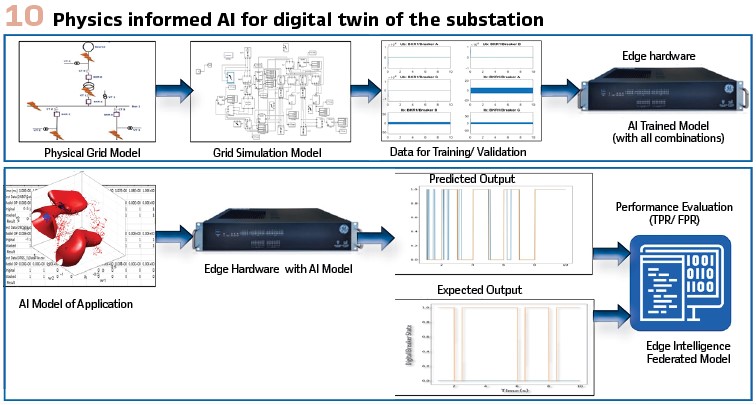
The real-time AI technology enabling localization, forecasting, detection, and neutralization – helping to facilitate reliable and safer operation of the grid substation.
Many critical infrastructures, such as electric power grids, are operated via central control systems, acting as the brain of the network through data collection from sensors. Given the critical nature of these assets, protection and safety of these assets are imperative.
Physics-informed technology is capable of not only detecting anomalies in the grid system but also localizing the anomaly and neutralizing their impact. With the modernization and digitalization of the grid, AI has the power (pun intended) to make great strides and address modern network challenges.
Conclusions
There is no question that grid is changing driven by decarbonization and electrification. Globally, the power grid industry needs more investment in grid modernization and the energy transition to allow more green electrons to flow while improving grid reliability, safety, sustainability, and affordability.
The many parts and pieces of today’s grid infrastructures are insufficient to integrate more renewable resources and maintain supply through extreme external conditions, such as heatwaves or storms.
To address these challenges and unlock innovative and disruptive solutions, utilities will be embracing digital transformation across transmission and distribution infrastructures. Distributed control at zonal substation level will be required for the grid resilience and stability with high-speed secured peer-to-peer communications. The digitization of data is integrating previously siloed data streams to provide new visibility into the overall health of critical power system assets.
Digital transformation of substations protection, automation and control systems with software-defined architecture allow flexibility required in the substations. With digitalized data availability in the substation, artificial or advanced intelligence can be used to adapt with changing grid conditions. Critical considerations and the role of AI in substations cannot be ignored. The question then turns to: how do we develop it responsibly? It’s clear that this is a powerful technology, so we need to stay ahead of the game and innovate with equal parts caution and optimism.
Biographies:

Dr. Mital Kanabar is a senior director of innovation in GE Vernova’s Grid Automation (GA) business based out of Grid IQ center in Markham, Canada. He has 15+ years of power industry R&D experience and holds holds 20+ international patent applications; and published more than 50+ journal/magazine/conference articles. Mital is also serving as a Vice-chair of IEEE PES PSRC Relaying Communication Sub-committee (H), and active contributors of CIGRE, and IEC working groups.

David MacDonald – After graduation from the University of Strathclyde, David worked in the utility industry, latterly as Protection and Control Standardisation Manager at Iberdrola´s DNO in Spain where he was responsible for the specification of automated configuration tools and specification and qualification of various device types. Since 2022, he is a Solution and Standardization Architect, working within the Office of Innovation at GE Grid Automation. He is convener of Cigre B5.84 Working Group.

Dr. Sean Norris is a Senior Innovation Application Architect with GE Grid Automation, based in Edinburgh, UK. Seán has over 10 years experience with GE in the field of wide-area control with a particular focus on frequency and transient stability and product development in these areas. He has experience across the technology development stages from innovation through to business-as-usual deployment. He is currently working on the next generation of zonal autonomous control within GE Vernova and is an active member in working groups for System Integrity Protection Schemes and Generator protection and control.