by Rich Hunt, Eric Udren, Juergen Holbach, Damir Novosel, Quanta Technology, USA
The electric industry has reached an inflection point for future architecture of protection, automation, and control (PAC) systems. Transformations to electric system operations include inverter-based resources (IBRs), new operating and ownership models, and new regulatory requirements. This requires PAC systems to be flexible and adaptable. At a high level, future PAC systems must:
- Support dynamic functional and setpoint evolution to address the impacts of inverter-based resources, distributed energy resources (DERs), and storage on the available short circuit current and power flows
- Automate compliance to new regulatory requirements placed on electric system operators to ensure the reliability of the system without adding additional workload on PAC engineers
- Seamlessly move data among different applications, devices, systems, substations, locations, and owners for dynamic functions, settings, automation, and management of PAC and grid systems.
This means the PAC industry must adopt the software-based and information technology (IT)-based model of digitization, digitalization, and virtualization as a path forward. The end goal for PAC is to focus human expertise on the activities that require it while automating monitoring and management tasks that can be handled with algorithms or artificial intelligence, while remaining focused on applications that have business value to utilities.
One of the challenges to adopting this new model is that workers need to acquire new skills and knowledge to face these new challenges, from specific software applications through IT and networking knowledge – growing the capabilities of the workforce must be part of the PAC transition.
It is important to keep in mind that the goal is to provide the flexibility, adaptability, and dynamic capability in the PAC system that meets future operating needs however they evolve. Taking the path we present here has inherent advantages. The first is that this approach leverages tools, techniques, and concepts already proven in other industries, lowering adoption risk. The second is that this approach meshes with the skillset and capabilities of the next generation of utility workers, who have grown up in the world of networked communications, modeling, and virtualization.
Impact of Changing Utility Operation
With the increased penetration of IBRs, it is necessary to address impact on PAC systems through digitization, digitalization, and virtualization. IBR impact examples are shown in Table 1. As more DERs using IBRs without inertia are deployed, system regions swing faster. Imbalance between generation and load causes faster frequency decline, resulting in the need to update underfrequency load shedding schemes or to transition to schemes based on direct power flow imbalance measurements.
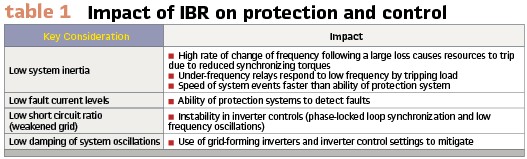
While conventional synchronous generators have operating reserve margins that naturally compensate for the imbalance, IBRs could react much faster than conventional generation in balancing load and generation but require use of digitization, digitalization, and virtualization technologies to automate and stabilize the process and test the PAC accompanying schemes. Firstly, reserve must be available, either through DER energy margins or through storage, to balance supply with load. Secondly, new sensors, algorithms, and tools must dynamically identify system needs and utilize those margins where needed.
Finally, fast control and protection actions using communications trigger actions to arrest frequency decline and return the system to stable operation.
Synchronous generators supply high fault current as their inertia dampens transient phenomena during short circuit events, allowing protective relays to operate reliably. IBRs do not significantly increase current during short circuits and cannot control the speed of transient phenomena, impacting PAC system reliability. This has been seen with the tripping of large amounts of solar generation due to faults on transmission systems, e.g., Southern California Solar Resource Loss, Aug. 2016; and ERCOT Solar Resource Loss, May 9, 2021, both with approximately 1.2 GW solar generation dropped. In both cases, IBR resources immediately and incorrectly detected voltage drop during normal fault clearing as a frequency event due to phase-locked loop detection techniques. NERC has been taking corrective actions in cooperation with IBR owners, who need to adapt IBR protection and control through proper measurements, detection methods, and testing – all as part of the digitization, digitalization, and virtualization process.
Moving towards the future PAC system
The first step to prepare for the future architecture is to digitize every analog interface, requiring a process interface for every piece of primary equipment and instrument transformer. The resulting digital data must use industry standard data models, such as those in IEC 61850, to efficiently share information among devices, applications, and systems. It is also important to think about digitizing out on the grid to acquire key data needed for PAC systems. For example, synchronized measurements gathered from circuit apparatus are used in new distribution protection schemes such as falling conductor protection and refined granular load shedding, as detailed in the DOE report on the Distribution Synchronized Measurements Roadmap.
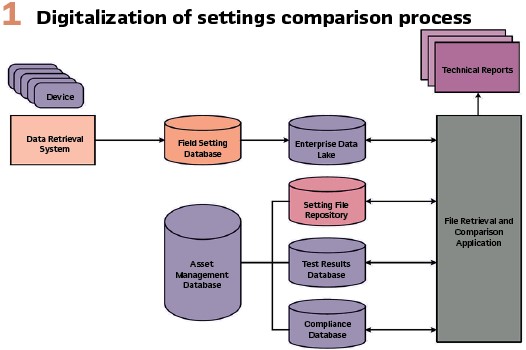
Digitalization is the process of converting existing architectures and functionalities into their digital equivalents by combining digitization of interfaces with algorithms and artificial intelligence to automate functions. One example of digitalization is protection settings validation, often needed to perform wide-area coordination studies to meet regulatory requirements. Figure 1 shows how software tools can automatically retrieve relay configuration files from the centralized settings repository, retrieve relay configuration files for the same devices directly from the field, and do a validation check to flag discrepancies, with the goal of establishing the single source of truth for in-service settings. Similarly, Figure 2 shows an automatic fault location system for both transmission and distribution networks that automatically retrieves data from protective relays, SCADA, reclosers, AMI, FCIs, and PMUs, and uses an expert system to accurately determine fault location based on available data.
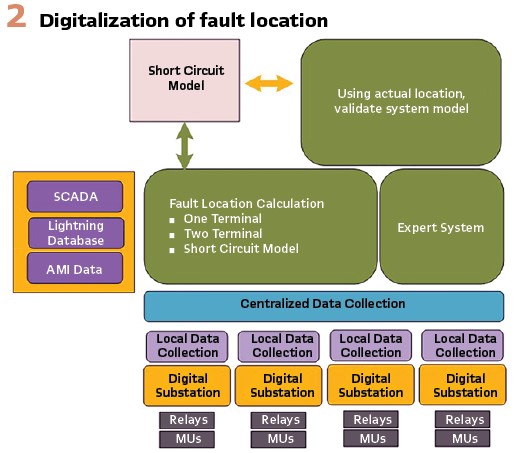
Substation-level digitalization: As digitalization progresses, the industry is creating the PAC architecture of Figure 3. At the substation level, time-critical functions like fault protection and local voltage control are performed by a high-reliability array of equipment consisting of algorithms running in multiple processing platforms sharing information and control commands with redundant merging units (MUs) used as process digitization interfaces connected through redundant Ethernet networks.
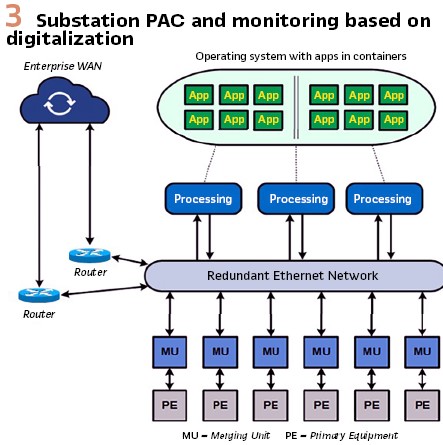
To holistically protect, control, monitor, and manage the wide-area grid, these substation-level PAC systems are being integrated into enterprise systems via wide-area networks (WANs) that interface to the substation network through routers with firewalls and other cybersecurity protection, also shown in Figure 3. Along with substation high-speed protection and control applications operating locally, other substation functions turn vast continuous streams of MU data into compact representations that are shared via enterprise communications for grid-level functions and virtualization. Examples of processed and shared information include familiar SCADA measurements and reports, alarms, sequence-of-events and oscillographic records, and power-quality or wideband waveform analyses and snapshots. This also includes synchrophasor measurements, with consistent waveform phase position reporting across the region, as the streaming analog data platform that will serve wide-area PAC functions.
Virtualization
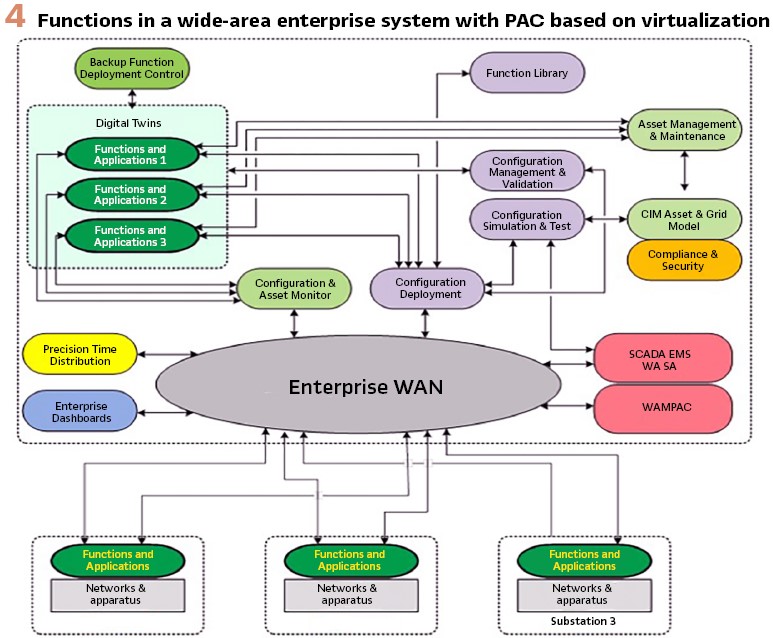
Wide-area PAC, monitoring, and management: Virtualization is directly turning functions and applications into software modules that process, analyze and act on digital data. Figure 4 shows an example of the enterprise-level or wide-area applications processing information from digitalized substations. While the functional diagram implies a physical center where all these applications are performed, the architecture is intended to distribute the functions across redundant processing arrays in multiple locations and with redundant WAN communications for convenient system maintenance operations on components as well as robustness against failures, errors, and disasters. The WAN-based distributed processing is well-suited for mission-critical WAMPAC functions like holistic voltage profile control, instability correction, or backup fault protection, all of which utilize control communications through the network to substations in tens of milliseconds or faster, readily achieved with today’s WAN services.
Other services and applications include:
- Wide-area distribution of sub-microsecond precision time signals, to support synchronized PMU measurements for WAMPAC applications without dependence on GNSS satellites for grid-wide coherency. Time distribution is designed into the WAN configuration as a core platform function with the sort of multi-source and multi-path redundancy and robustness we design for fault protection and control functions
- Grid monitoring and control applications advanced beyond today’s SCADA and EMS practices, using new high-resolution synchronized measurements
- Configuration management and backup for applications and communications elements of the entire wide-area PAC system
- Diagnostic, maintenance, and asset management functions based on virtualized models of the grid and its PAC system
- Application and configuration development and deployment systems which can upgrade or evolve the functionality of any part of the PAC system, including off-line validation of changes and deployment updates to operating systems without disrupting grid operations – like an airplane forever maintained in flight
- A management function grouping that includes grid and PAC key performance indicator dashboards, business performance measurements, strategic asset management and maintenance support, and exceptional situation handling
Virtualization Platform and Digital Twins: The performance of functions and applications listed can only be achieved or assessed if there is a basis of expectation of behavior of the grid and its PAC system under the conditions of each moment. As PAC evolves into the era of virtualization, every functional aspect of the grid and its PAC system is to be embodied in a model – a computer-based or virtual representation which can be stimulated with inputs simulating those of the actual grid; the outputs from the model and its dynamic performance are then used to assess whether the functional element is performing as needed. More importantly, this stimulation and observation of models can be used to assess performance in complex future or contingency situations never previously experienced, for which correct and efficient performance are essential. The ensemble of virtualizations is operated as a complete model of the grid-and-PAC system for study of historical or projected operating conditions. This enables development, validation, and deployment of updated or new settings and functions in stages as legacy elements are successively removed from service. The entire updating process has been validated for security with virtualizations before deployment in the operating PAC system.
Virtualizations or models of specific PAC and grid elements are now often described as digital twins. Digital twin models have the same inputs, outputs, settings, and functional behavior as the objects for which they serve as twins. Interconnections of digital twins can simulate the performance of the real-world assets they mirror, as explained above. They also can embody the configuration – all the settings, interconnections, and asset history – of the real-world assets and can thus document the correct and effective configuration of the operating PAC system and grid. Beyond this, real-world or modeled event sequences can be processed by digital twin interconnections to analyze or forecast misoperations, or end of asset life. Digital twins are often described as existing in a WAN cloud remote from the mirrored physical objects, but the cloud can be the distributed WAMPAC platform characterized here.
There are numerous uses of digital twins already in use, including PAC systems with mirrored cloud configurations of IEC 61850 Logical Nodes and SCL configuration, dynamic three-phase short circuit models, and asset tracking and asset management models. One use of a digital twin for managing IBRs is to operate dynamic models of the transmission and distribution systems using real-time measurements. The digital twin can be used to identify and control abnormalities caused by high penetration of IBRs and DERs.
The same model could be used to dynamically determine the appropriate protection settings for changing levels of available fault current and roll out these settings to protection devices in real time.
Moving Forward from Today
Digitization, digitalization, and virtualization are the future of PAC systems. This process brings major changes in how the utility designs installations and operates the PAC system. The transformation will affect many enterprise activities tied to the planning, design, construction, operation, maintenance, asset management, and financing of transmission substations. Experience has already shown that without attention to this transformation of activities, the benefits of digitization will not be achieved.
The first task for successful adoption of the new digitalized PAC system approach is training the existing workforce to acquire new expertise. Recruiting of new resources must specify the needed new skill sets. PAC technicians and engineers must have a deep understanding of how to configure and maintain communications equipment, including switches, routers, and real-time clocks.
The settings and configuration of the communications equipment are integrated with PAC settings and must be handled and managed as such. The IT department must support the protection system and deploy operational communications systems that meet PAC requirements for performance and redundancy in the future.
The second task for successful adoption of the new digitalized PAC system is to ensure that every operating group involved in equipment and system operations is engaged in the design and discussion process through either formal or ad hoc working groups. All groups must understand how their evolving operations and activities will impact or change the skills and training needs for their own team members and those of other groups.
A key part of successful adoption is rigorous testing of the resulting PAC system and system components. This requires creating test plans, test conditions, and expected test results for design testing, acceptance testing, and commissioning testing. A fully virtual PAC system such as in Figure 4 will use digital twins to test new applications, installations, or configurations with a robust testing routine, or even operating as a shadow system and validating performance via digital twins with live data.
Testing of digitized or digitalized designs: The first systems a utility is likely to install are digitalized systems, still relying on communications between individual functional devices and applications. Since the interfaces between devices are simply communications, these systems will use standard designs and templates. Engineers must then become familiar with new tools and learn to design and document virtual protection and control systems. Utilities must invest in the development of the new standard schemes, which may be more expensive for the first applications compared with building a conventional design. However, the standard digitalized design becomes a template that can be reused with minimum effort and cost for successive PAC projects. This standard template needs a rigorous quality assurance process along with inclusion of foreseen standard options during development to ensure error-free and convenient reuse during its service life.
Good practice is to test each standard design in the laboratory environment. The test setup should mirror the exact hardware and functions as they will be used in the PAC scheme for which the standard was developed. The template can be tested for a pilot project with expected options or variations. A real time digital simulation system performing hardware-in-the-loop (HIL) testing provides the most efficient testing arrangement for such complex schemes. In time this development environment will be absorbed into the virtualized wide-area management system for PAC.
The test setup or its virtualization should also be used to conduct hands-on training for protection, commissioning, maintenance, and communications technicians and engineers on the digitized PAC schemes. This will allow the technicians and engineers to acquire needed expertise in the new technology, and familiarity with design features and options.
New maintenance and test procedures are validated with failure simulations. Personnel will later be effective in working on actual systems in service.
Conclusion: Digitized and digitalized wide-area systems with virtualization of PAC functions and grid models are the future of PAC. These systems present utilities with the only affordable path to flexibility and adaptability that accommodates the changes in power flows, short circuit and inertia levels, operating models, and ownership models coming to the electric utility industry. These systems can dynamically initiate control actions and adapt protection settings and functions based on the status of the system, and can test them automatically, as they roll out new wide area protection and control schemes.
Validation of new controls, settings, schemes, and PAC configuration versions can be carried out in a virtual or digital twin environment before they are deployed automatically across the grid, as it continues in normal operation.
Biographies:
Rich Hunt – Executive Advisor, Protection, Control & Automation, has over 30 years of experience in the electric power industry, emphasizing protective relaying. Over the last 15 years, his focus has been on all aspects of specifying and designing digital substations. He earned his BSEE and MSEE from Virginia Tech, is a Senior Member of IEEE, a member of the Main Committee of the IEEE Power System Relaying & Control Committee and is a registered Professional Engineer.
Erik Udren is Executive Advisor with Quanta Technology. He has a five-decade career in design and application of protective relaying, substation control, communications, and synchrophasors in T&D applications. He is Life Fellow of IEEE and active leader in IEEE PES PSRC and Communications and Cybersecurity Committees, IEC TC 95 relaying standards, IEC 61850, and NERC. He was Industry Guru in the September 2016 issue of PACworld and is a frequent contributor. In 2019, he was elected to the US National Academy of Engineering.
Damir Novosel is president and founder of Quanta Technology. Previously, he was vice president of ABB Automation Products and president of KEMA T&D US. Dr. Novosel is also an adjunct professor of Electrical Engineering at North Carolina State University. Damir, US National Academy of Engineers member and IEEE Fellow, served as president of the IEEE Power and Energy Society, VP of Technical Activities, and received the Patrick P. Ryan Meritorious Service award. He is IEEE PES Executive Advisory Council secretary and member of the IEEE Standards Association Standards Board and Strategic and Emerging Standards Committee chair. He received the CIGRE Attwood Associate and the Distinguished Member awards. Damir holds 18 patents and was selected Mississippi State University Distinguished Engineering Fellow.
Erik Udren – Executive Advisor, Senior Director of Automation & Testing., has more than 25 years of experience designing and applying protective relaying. An IEEE member and chairman, he has published over a dozen papers and holds three patents. In 2009, Juergen received the Walter A. Elmore Best Paper Award from the Georgia Tech Relay Conference.